Emerging trends in building design, technologies, and materials
On this page
The global construction industry is undergoing rapid changes due to the adoption of innovative design approaches, technologies, and materials. These trends present an opportunity for New Zealand’s construction sector to improve its performance, regulations, and quality standards by learning from the best practices of other countries. This section provides an overview of key innovation trends currently reshaping the global construction landscape. It also features local examples applying and adapting these trends.
Building design: A shift towards low-carbon, sustainable principles
To prevent the worst consequences of climate change, humanity needs to limit global temperature increase to 1.5°C. New Zealand has committed to this goal under the Paris Agreement, aiming for net-zero carbon emissions by 2050 (Climate Commission, 2023).
However, the 2022 Global Status Report for Buildings and Construction revealed that the sector has fallen behind on its decarbonisation target for 2050 (United Nations Environment Programme, 2022). In 2021, the sector accounted for more than 34% of global energy demand and 37% of energy and process-related CO2 emissions. The sector’s operational energy-related CO2 emissions continued to climb, rising 5% since 2020 and 2% above pre-pandemic levels. In New Zealand, the Building Research Association of New Zealand (BRANZ) estimates that buildings contribute directly and indirectly to up to 20% of the country’s total greenhouse gas emissions (BRANZ, n.d.).
The UNEP report calls for a fundamental shift within the sector, aligning with the Paris Agreement’s objectives. Achieving this goal requires prioritising innovative building design principles such as net zero (operational) carbon, regenerative, passive and biophilic design.
Net-zero (operational) carbon buildings offset their emissions throughout their lifespan.
These buildings achieve this by combining energy-efficiency with reliance on renewable energy sources, either on-site or off-site (World Green Building Council, 2018). In essence, they operate without producing any net greenhouse gas emissions.
The number of net-zero carbon buildings is expanding. In 2019, the New Building Institute identified 580 certified, verified, and emerging projects (Hobart, 2019). By 2023, this figure has climbed to roughly 856 certified net-zero buildings worldwide, as documented in the World Green Building Council’s Advancing Net Zero Status Report (World Green Building Council, 2023).
In New Zealand, the Building for Climate Change (BfCC) programme aims to achieve “near zero carbon” buildings by 2050 (MBIE, n.d.), which is a way to enable “net zero carbon” buildings. Near zero (or net-zero ready) buildings have minimal embodied carbon and are highly energy efficient, with the remaining emissions easily offset. The government aims to reduce building-related emissions by 0.9Mt – 1.65Mt CO2-e (million tonnes of carbon dioxide equivalent) in the 2022-2025 period (MBIE, 2023).
Measuring carbon emissions of buildings is a crucial tool for informing sustainable design choices and aligning with decarbonisation goals.
By comprehending a building’s environmental impact throughout its entire lifecycle, from materials to operations, designers and owners can make informed decisions that minimise its carbon footprint and contribute to a sustainable future.
The Life Cycle Assessment (LCA) approach provides a standard framework for this analysis. It takes into account both embodied carbon (generated by the production and transportation of building materials) and operational carbon (arising from the building’s energy use during its lifetime). To aid architects, engineers, and designers in this task, numerous carbon measurement tools have been developed in recent years, offering insights into assessing and reducing building emissions.
In New Zealand, BRANZ created tools like LCAQuick: Life cycle assessment tool and LCAPlay: Options assessment tool, to help with low-carbon design (BRANZ, n.d.), while the New Zealand Green Building Council (NZGBC) released embodied carbon resources and the Green Star NZ certifications (New Zealand Green Building Council, n.d.). Green Star NZ is a nationally recognised rating tool that assesses buildings across categories like energy, water and embodied carbon.
Table 1 shows the growing number of buildings with environmental certifications from the NZGBC since 2020. These include Green Star NZ, National Australian Built Environment Rating System (NABERS) NZ, and Homestar- all evaluating the sustainability performance of buildings. Since 2020, all 4 certifications showed growth – 34% increase in 2021 and 50% increase in 2022. Green Star NZ recorded the highest increase, from 21 in 2021 to 88 in 2022. This can be attributed to the government’s preference for Green Star NZ as a sustainable building rating tool due to its specific adaptations to the New Zealand context and its market maturity (MBIE, 2022b). The NZGBC also recently introduced the Net Zero Buildings certification, a voluntary certification that tracks major sources of carbon emissions in building operations, including energy, water, waste, and refrigerants (New Zealand Green Building Council, 2023).
Table 1: Number of Buildings with NZGBC Certifications (2020 to 2022)
Year |
Green Star NZ registrations |
NABERSNZ certifications |
Homestar registrations |
Homestar Built Ratings |
Overall growth |
2020 |
21 |
53 |
4754 |
960 |
Baseline |
2021 |
54 |
72 |
5960 |
1689 |
⇑ 34% |
2022 |
88 |
116 |
6315 |
2150 |
⇑ 50% |
Source: NZGBC 2023
Chapter 12 of the New Zealand Emissions Reduction Plan outlines key government initiatives to promote sustainable construction and net-zero carbon buildings, spearheaded by the BfCC programme (Ministry for the Environment, 2022). BfCC focuses on (MBIE, n.d.):
- Regulatory changes which aim to enhance operational efficiency and reduce the whole-of-life embodied carbon of buildings. This might involve mandatory reporting requirements, carbon caps for new projects and a review of the role of sustainable building rating systems (New Zealand Government, 2021).
- Legislative reforms, specifically the proposed amendments to the Building Act 2004, which seeks to embed carbon reduction and operational efficiency in new buildings. They also introduce national waste minimisation requirements, mandatory energy performance ratings and waste minimisation plans for specific construction and demolition activities. (MBIE, 2023b). These changes will be implemented gradually after public consultation.
- Non-regulatory incentives which encourage voluntary emissions reduction in both new and existing buildings.
Complementary initiatives include:
- The Accord’s Carbon Waste Measurement Tools Initiative which supports the development of carbon and waste measurement tools and resources, empowering businesses to assess and address their environmental footprint (Construction Sector Accord, 2023c).
- The Carbon Neutral Government Programme which requires minimum Green Star ratings for new non-residential government buildings: 5 stars from April 2022 for projects over $25 million and 5 stars from April 2023 for projects over $9 million (New Zealand Government, 2021).
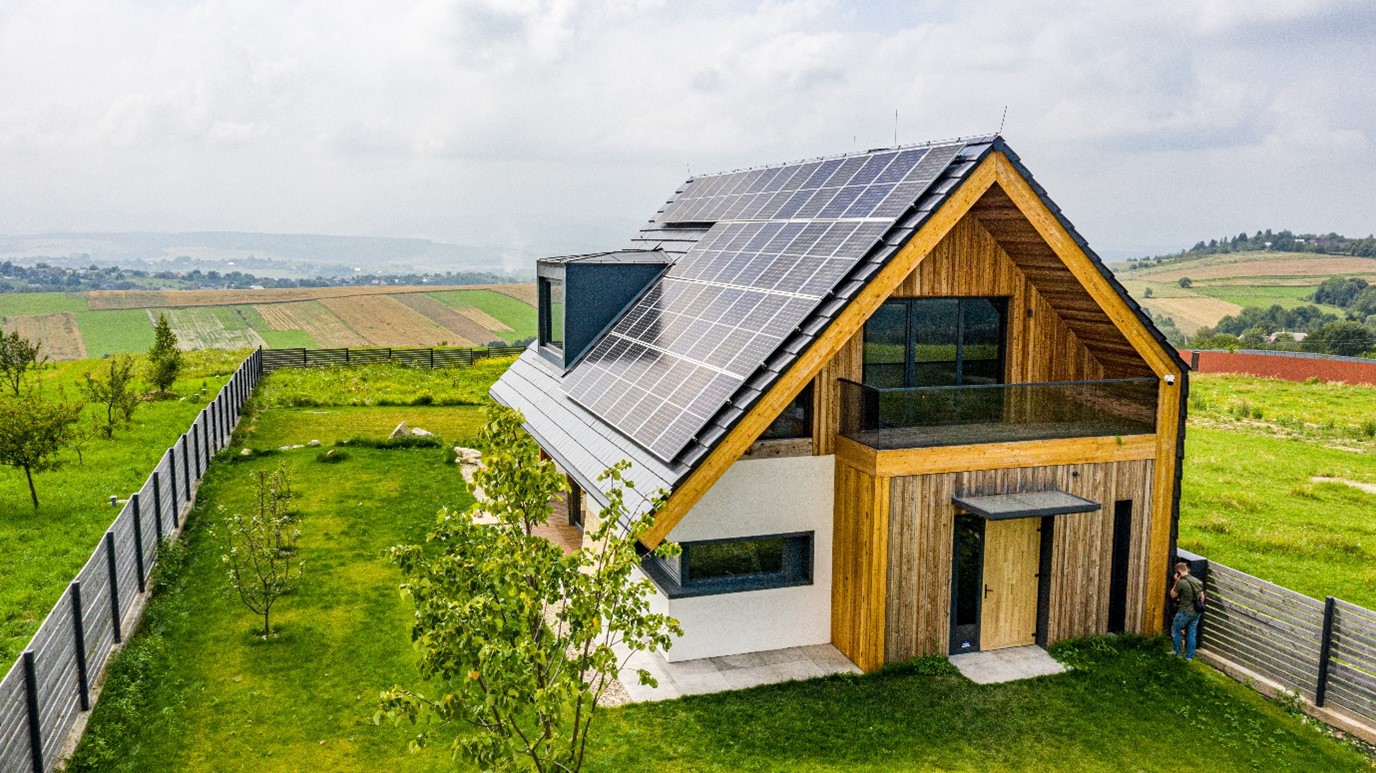
Regenerative design builds structures that actively boost the health and well-being of both people and the environment.
Architects and designers are embracing this philosophy to reverse the impacts of construction on the environment (Bauhaus Earth, 2023). Key strategies used in regenerative design include: harnessing renewable energy sources (such as solar and wind power); capturing and reusing water (through rainwater harvesting, greywater recycling, etc.); waste reduction and resource recovery (by incorporating composting systems, recycling facilities, etc.); and using non-toxic, low-impact materials to enhance indoor air quality and protect building users from harmful substances (National Institute of Building Sciences, 2023).
The International Living Future Institute is a leading organisation that promotes regenerative buildings. Its Living Building Challenge certifies structures that meet exceptional standards of sustainability, health, and equity (International Living Future Institute, n.d.). In New Zealand, regenerative design has been combined with indigenous creativity and Te Ao Māori to create living buildings like:
- Te Kura Whare, which showcases the Tūhoe culture and features a café, library, sacred archives and grand Tribal Chamber and amphitheatre for community events (International Living Future Institute, 2022).
- Te Wānanga o Raukawa (Ōtaki campus), which operates entirely on solar power, captures and uses rainwater, and treats wastewater on-site, while supporting native plant life around the structure. (Te Wānanga o Raukawa, 2022).
- The Living Pā, which is expected to be completed in 2025 and will be waste-free, net-zero energy and water, and made of non-toxic materials (Victoria University of Wellington, 2023).
Passive buildings are gaining traction worldwide, including in New Zealand.
These buildings minimise energy consumption by using techniques such as insulation, airtightness, ventilation, and passive solar to reduce the need for additional heating and cooling (Anand, Kadiri, & Putcha, 2023).
The Passive House standard is one of the most widely used standards for passive building design. There are over 70,000 Passive House buildings worldwide that meet rigorous standards not only for energy efficiency but also for comfort and quality (Frew, n.d.).
In New Zealand, Kāinga Ora has built several passive houses, including the Bader Ventura Development in Auckland, the first government-funded Passive public housing project in Australasia. It comprises 18 passive house apartments designed to slash energy use and heating and cooling costs to just $1 a day (Kāinga Ora, 2023). Another example is the Toiora High Street Cohousing in Dunedin, New Zealand’s largest Passive House project to date and the first multi-unit Passive House residential dwelling that features a mini village of 21 homes (Sustainable Engineering Ltd, 2023).
Biophilic design is another growing architectural trend that connects humans and nature within buildings.
It involves incorporating natural elements into buildings to improve occupant well-being and promote sustainability. Biophilic design has gained global attention as more evidence has shown its benefits in reducing stress and anxiety, boosting mood, and improving cognitive function and creativity. (Zhong, Schröder, & Bekkering, 2022).
Biophilic design can resemble nature, traditional architecture, or cultural heritage, using symbols, shapes, colours and materials. It can also incorporate natural elements like plants, water, light, ventilation and views into the structure (Grazuleviciute-Vileniske, Daugelaite, & Viliunas, 2022).
Building technologies: Integrated solutions for efficiency, productivity, and safety
Emerging technologies such as Building Information Modelling (BIM), artificial intelligence (AI), virtual reality (VR), augmented reality (AR), construction robots, and modern methods of construction – have the potential to greatly improve the way buildings are designed, built, and managed. While these technologies have been used independently in the past, a recent trend is their increasing integration, to create an even more profound impact on the industry.
Building Information Modelling (BIM) is combined with other emerging technologies to amplify its capabilities.
BIM in New Zealand defines BIM as “a coordinated set of processes, supported by technology that add value through the sharing of structured information for buildings and infrastructure assets” (BIMinNZ, 2016). It has been used in the global construction industry for more than a decade, and its adoption has grown rapidly. In New Zealand, for example, the use of BIM on construction projects has expanded from 34% in 2014 (when the BIM Acceleration Committee was established), to 70% in 2021. Within that period, BIM’s use has extended across all stages of the project lifecycle, from planning and designing to construction and operation. According to the BIM Benchmark Survey in 2021, the key benefits derived by industry and subcontractor groups from its implementation include enhanced coordination, improved clash detection, and optimised cost and resource efficiency (EBOSS, 2021a)
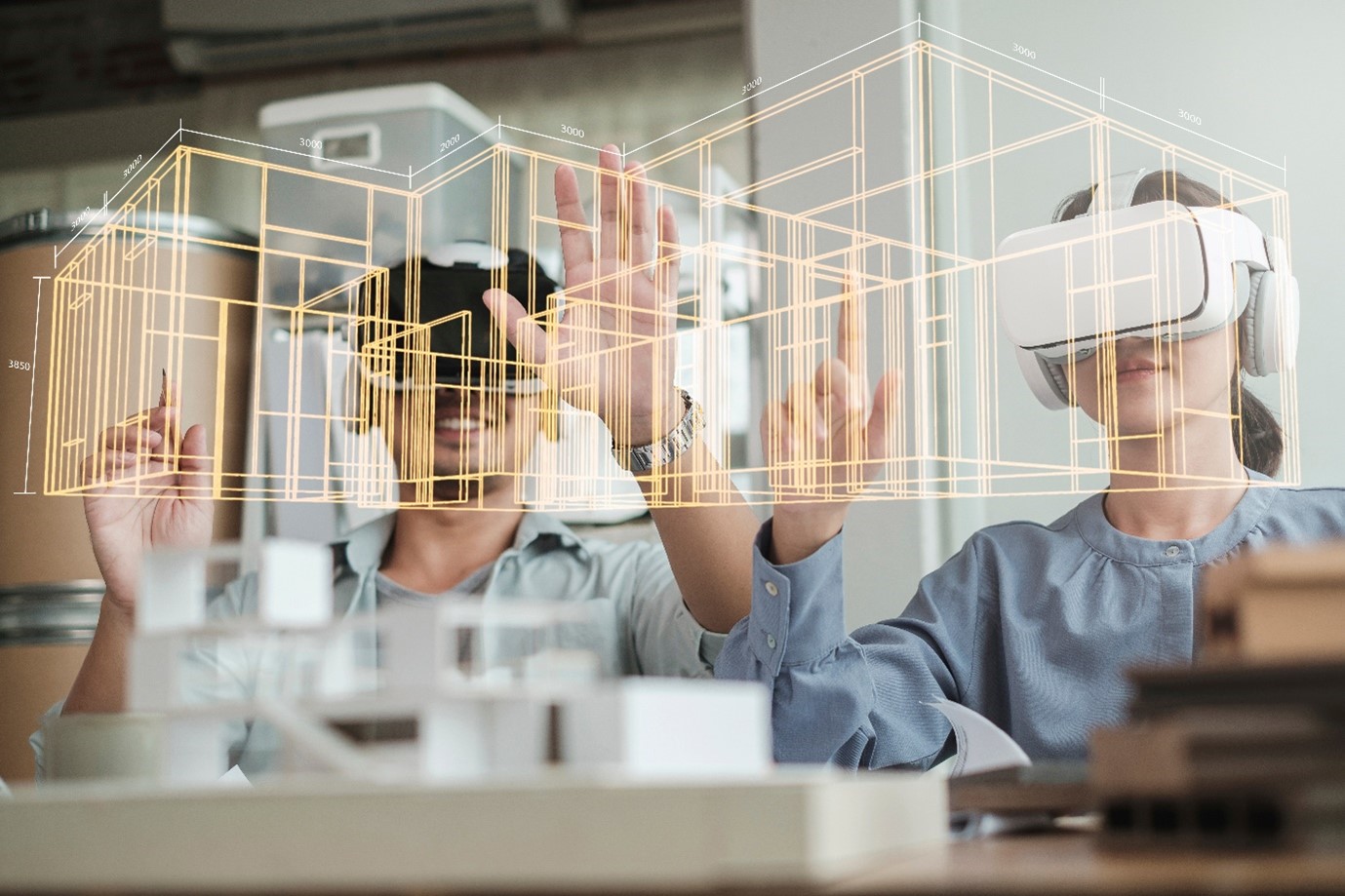
Several companies around the globe are integrating BIM with artificial intelligence and machine learning to achieve enhanced design, quality, and efficiency (Pan & Zhang, 2022; Wang, Zhou, & Li, 2020); improved productivity and safety on site (Chen, Zhang, & & Hu, 2022; Zhang, Liu, Hu, & Zhang, 2022); and better project coordination and collaboration (BIM and Beam, 2023; Owen, 2023). Others are integrating BIM with VR and AR to visualise building appearances before construction and allow early identification and rectification of design issues (Potseluyko, Rahimian, Dawood, Elghaish, & Hajirasouli, 2022) and train workers using simulated tasks in a safe environment (Site Safe NZ, 2023).
In New Zealand, the Accord, BIMinNZ and NZIOB are working together to create the Construction Digital and Data Roadmap, to foster widespread digital tool adoption. The five-year roadmap features initiatives like BIM / digital engineering resources for clients and designers, aiming to propel the industry towards optimised efficiency, data-driven decision-making, and sustainable practices.
Construction robots are gaining traction due to their potential to significantly improve productivity and enhance safety within the industry.
Over the past decade, leading nations in this field, like the United States, China, India, Singapore, and Canada have developed robots capable of automating repetitive and labour-intensive tasks, including laying bricks (FBR, 2023); tying reinforcing steel (Advanced Construction Robotics, 2023); and cutting, drilling, sanding, and transporting materials (Baubot, 2023). There are also robots that can build 3D maps and monitor potential hazards in construction sites (Naska.AI, 2023) and those that can be worn (like an exoskeleton), capable of supporting and protecting workers while they perform physical and demanding tasks, such as carrying heavy objects (Ekso Bionics, 2023).
Modern Methods of Construction (MMC) boost quality, efficiency, and sustainability in construction projects.
These innovative techniques, including prefabrication, modular construction, and 3D printing, deliver high-quality, cost-effective and sustainable buildings.
Prefabrication and modular construction, collectively known as offsite manufacturing (OSM), involve manufacturing prefabricated elements offsite and assembling them on-site. This approach is gaining momentum, with the global market for prefabricated construction projected to reach $157 billion by 2023 (Utilities One, 2023). Countries like Japan and Sweden are leading the way and New Zealand is rapidly embracing this innovative approach.
XFrame, developed by a doctoral student at Victoria University of Wellington, addresses key challenges in construction: efficiency, sustainability, and adaptability. This modular building system features easy installation and removal of panels, enabling rapid reconfiguration of buildings. Lightweight and flexible framing allows for customised designs and layouts, while circular economy design promotes component reuse and recycling (Intellectual Property Office of New Zealand, n.d.).
The New Zealand government is actively promoting the adoption of MMC to address the country’s growing infrastructure demands. Key initiatives driving increased MMC uptake in the construction industry include:
- Streamlined consenting: Building Act 2004 amendments pave the way for offsite manufacturing and prefabrication by simplifying approvals for innovative and efficient building methods (MBIE, 2022c).
- Collaborative innovation: The Infrastructure Action Plan 2023 unites industry experts, research, and academia to develop a market strategy and boost MMC innovation (The Treasury, 2023d).
- Quality assurance: The Building (Modular Component Manufacturer Scheme) Regulations established a voluntary certification scheme for manufacturers, building trust in MMC products and streamlining approvals (MBIE, 2022d).
- Government-industry collaboration: Accord-led MMC forums address the Commerce Commission's recommendation for a coordinated approach (Commerce Commission, 2022). The government forum focuses on Crown projects, while the industry forum (co-led with OffsiteNZ), develops tools and resources to enhance MMC adoption across the sector (Construction Sector Accord, 2023a).
3D Printing is another MMC technique that is growing rapidly due to benefits of time and cost savings, as well as reduced waste.
It uses materials like concrete, metal, and resin to build entire structures or components for houses, bridges, etc. The global market for 3D-printed construction is expected to rise from USD3.42 billion in 2022 to USD519.49 billion by 2032 (Precedence Research, 2023). This growth is fuelled by factors such as affordability and sustainability and technological advancements. Research shows that 3D printing can slash construction waste by 60%, production time by 70% of production time, and labour costs by 80% (Ranjha, Kulkarni, & Sanjayan, 2018).
New Zealand’s Qorox became the first in Australasia to implement building code-compliant concrete 3D printing solutions. It also constructed NZ’s first fully 3D-printed home (Property & Build, 2023).
Building materials: Embracing circular economy through reuse, renew and reduce practices
The construction industry is a significant contributor to global greenhouse gas emissions, with building materials accounting for a substantial portion of this impact. To achieve net-zero emissions from the built environment sector by 2050, a shift in how we procure and use building materials is essential.
A recent report entitled Building Materials and the Climate: Constructing a New Future, jointly developed by the United Nations Environment Programme (UNEP) and Yale Centre for Ecosystems and Architecture, highlights the urgency of decarbonising building materials. The report proposes a transition to regenerative material practices that prioritise the use of earth- and bio-based materials (United Nations Environment Programme, 2023). These naturally derived materials have low environmental impact, have the potential to store carbon, and contribute to biodiversity preservation.
The growing awareness of waste as a valuable resource resonates with New Zealand’s construction sector. Industry leaders are increasingly aware of the reputational risks associated with wasteful practices and are embracing concepts such as the circular economy, which promotes resource conservation and waste reduction (Construction Sector Accord, 2023b).
In a collaborative effort, the Accord and the Sustainable Business Network hosted a cross-industry workshop, under the Sustainable Construction Cross Sector Forums initiative, to identify the root causes of construction waste using circular economy principles. Workshop participants identified 5 priority areas for addressing construction waste. 3 of these priorities - integrated design, reverse logistics and product stewardship - have led to the formation of industry action groups. The remaining 2 priorities - information and knowledge sharing - were identified as enabling projects that will be spearheaded by the Accord (Construction Sector Accord, 2023c).
Earth-based materials are made from soil, such as clay, sand, gravel, or silt.
They can be used to create various building materials such as rammed earth, compressed earth blocks and clay plasters. Earth-based building materials have enormous potential as solutions for low-energy dwellings, energy efficiency, thermal comfort, eco-architecture, climate responsiveness, affordability, and recyclability (ScienceDirect, 2022).
Despite the benefits of earth-based materials, they are not widely used in many countries, including New Zealand. A 2022 study by Massey University and Otago Polytechnic found that only 1% of houses in the country are earth buildings (Samarasinghe & Falk, 2021). The study identified several barriers to the growth of the earth building industry in New Zealand, such as: lack of awareness about the advantages of earth building; high cost and time of construction compared to conventional methods; limited availability of skilled labour and quality materials; regulatory hurdles and compliance issues; and negative perceptions and stereotypes associated with earth building.
Bio-based materials are made from living organisms, such as plants, animals and fungi.
They can be used to create various building products such as insulation, structural elements, or packaging (Hookham, 2022). Bio-based materials have low environmental impact and high biodegradability. They can also reduce the dependence on fossil fuels and synthetic materials. Some examples of bio-based materials are straw, mass timber and hempcrete.
Straw is a bio-based material that has been extensively used throughout human history and has seen a revival in recent years.
It is readily available and easily sourced, offering a cost-effective alternative to traditional building materials such as concrete, steel and brick (Yin, Yu, Ma, Liu, & Yin, 2023). Insulation materials made from straw are increasingly recognised due to their superior hygrothermal properties, low life-cycle costs, and low carbon footprint (Zhuo, Trabelsi, & El Mankibi, 2022). When used appropriately in construction, straw bales provide high levels of insulation and can help keep a home quiet and warm in winter and cool in summer. Straw bales have low embodied energy and are a renewable or sustainable building product (BRANZ, 2010).
Research on straw materials has advanced significantly over the past few years, leading to the development of new straw-based materials with enhanced properties. These materials offer promising solutions for sustainable construction due to their lower environmental impact, higher economic viability, and greater social acceptability compared to other conventional alternatives, such as cement, steel and wood (Yin, Yu, Ma, Liu, & Yin, 2023). Innovative straw-based materials that have been developed include straw fibre concrete, straw biomass ash and straw building panels.
New Zealand has an abundance of underutilised straw, capable of constructing the walls of approximately 2000 stand-alone houses annually (Hall, 2019). Strawlines, an innovative modular housing system, proposes to use straw and timber prefabricated panels to deliver affordable, low carbon homes to communities in Te Tau Ihu (Fineline Architecture, 2022). Hiberna Modular, another New Zealand company, has improved straw bale construction with its new Structural Insulated Panels (Hiberna Modular, 2023). These panels capitalise on straw’s inherent advantages, including strength, fire resistance, moisture control, insulation and a low environmental impact.
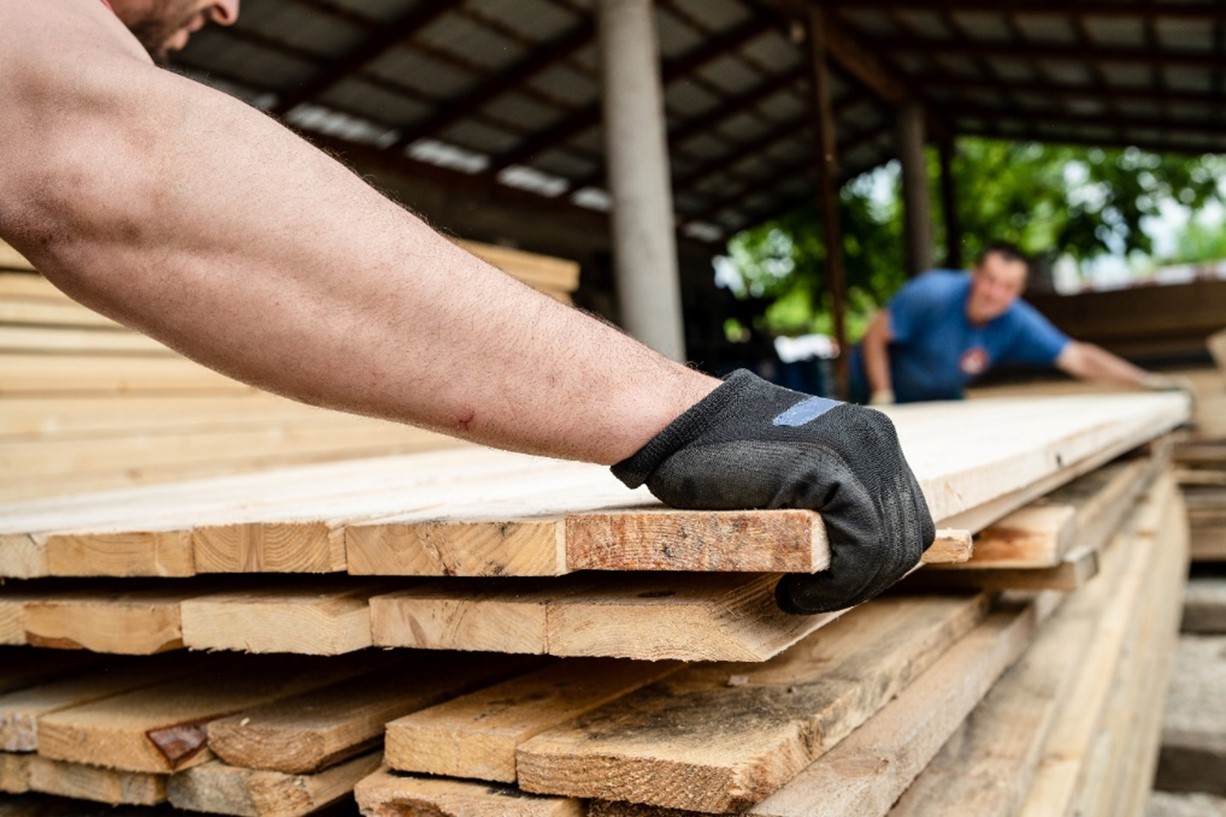
Mass Timber are wood products used in medium and high-rise buildings and construction projects.
These products include cross-laminated timber (CLT), glulam and laminated veneer lumber (LVL), derived from trees such as oak, bamboo, cherry, cedar, mahogany and birch. They are a sustainable and renewable alternative to traditional building materials such as concrete and steel. In 2021, the global mass timber construction market was valued at $857.1 million but is project to reach $1.5billion by 2031 (Allied Market Research, 2023).
Although New Zealand has an abundant forest resource, wood is rarely used in commercial and institutional scale construction (Ministry for Primary Industries, 2022). The use of wood in the country has only been growing at an estimated 1% per year, and New Zealand lags behind countries like Australia, Austria, Canada, Germany, and the United States, in the use of mass timber. To accelerate the construction industry’s use of wood and mass timber, the government has partnered with Red Stag Investments Limited to implement the Mid-Rise Wood Construction programme. The programme is expected to deliver economic benefits, with net value of $155 million by 2023 and $330 million by 2036.
Notable mass timber projects include the Clearwater Quays, New Zealand’s first mass timber mid-rise apartment building (WoodWorks, 2023) and the Tauranga City Council building, set to become New Zealand’s largest mass timber office building (Tauranga City Council, 2023).
Hempcrete, a mixture of hemp hurds (the inner part of the hemp stalk) and a lime-based binder, is emerging as a promising bio-based material for insulation and moisture regulation in buildings.
Despite its growing popularity globally, hempcrete construction in New Zealand has been limited due to obstacles such as the lack of a local hemp fibre processing facilities and the absence of an NZ-certified hempcrete binder (Hemp Building Association New Zealand, 2021). However, recent developments such as the opening of a decortication plant in Christchurch and the invention of Geobind hemp-binder by a local builder are seen as a game-changer by the emerging hemp construction industry (Jensen, 2022). These new developments will enable builders to source hempcrete locally, instead of importing it from overseas.
Low carbon concrete has the potential to make a significant contribution to reducing greenhouse gas emissions.
According to the United Nations Environmental Programme (UNEP), 30 billion tonnes of concrete are used each year, and the demand is expected to further increase due to population growth, urbanisation and infrastructure development. To achieve net-zero emissions by 2050, there is an urgent need to reduce emissions associated with concrete production and use.
In August 2023, Concrete New Zealand released a Roadmap to Net-Zero Carbon Concrete, mirroring a similar publication by the Global Cement and Concrete Association in 2022 (Concrete New Zealand, 2023). Both roadmaps focus on strategies such as reducing emissions from cement and clinker production, recarbonation and more efficient concrete design. They also require that over 30% of the emissions savings to achieve net-zero concrete must come from carbon capture and storage (CCS) technology, which is not yet commercially viable anywhere in the world.
Green concrete is a type of low-carbon concrete that has minimal environmental impact compared to traditional concrete (A. Sivakrishna, 2020).
This reduced environmental footprint comes from minimising energy consumption, carbon dioxide emissions and natural resource depletion, associated with concrete production and use. Cement, the component of concrete with the largest carbon footprint, can be partially replaced with alternative, lower-carbon materials to effectively reduce concrete’s emissions.
Supplementary Cementitious Materials (SCMs) have been used for decades worldwide as viable alternatives to cement.
Examples of SCMs are pulverised fly ash (waste from coal-burning power stations) and ground granulated blast furnace slag (waste from steel manufacturing plants) (Concrete New Zealand, n.d.). While not widely used in New Zealand, these materials are becoming more common in concrete mixes offered by mainstream concrete providers like Firth and Allied Concrete. In 2023, Holcim, one of New Zealand’s cement suppliers, established a facility in Auckland to import their ECOPlanet cement mixes, which incorporate SCMs, increasing their availability in the country (Holcim NZ, 2023).
However, the global supply of SCMs is projected to decline over time as the industries from which they arise become less prevalent. Recent studies indicate that global supply is already constrained to such an extent that importing SCMs for use in New Zealand may not result in a significant reduction in global emissions (Institution of Structural Engineers, 2023). Alternative SCMs available in New Zealand include calcined clay, silica fume, and natural pozzolans which offer domestic supplies of potential SCMs. Despite research into their performance by Concrete New Zealand, these materials are not yet available at a commercial scale.
In addition to using SCMs, other ways to green concrete include using recyclable and reusable materials. Concrete is often made with aggregates, which are the coarse and fine particles that make up the bulk of the material. Traditionally, aggregates have been quarried from natural sources, but there is a growing movement to use recycled and reusable materials instead. This can include paper or fibre, plastic waste, post-consumer glass and concrete debris. Using recycled materials reduces the need to extract virgin materials from the environment, saving energy and reducing emissions. Another way is using bio-concrete which is a type of concrete the uses bacteria to heal cracks in the material. The bacteria are added to the concrete mix, and when they come into contact with water and oxygen, produce a substance that fills the cracks. This can help to extend the lifespan of concrete structures and reduce the need for repairs.
Neocrete, a New Zealand company, has developed products that can help to green concrete (Neocrete, 2022). D5 Green reduces the water permeability of concrete, allowing for a reduction in cement content without loss of strength. It reduces carbon emissions and improves the performance of the concrete. Neocrete Activator increases the strength and durability of concrete and can also help reduce the amount of water needed to make concrete.
New Zealand pours 4 million cubic metres of concrete each year, producing 1.4 million tonnes of greenhouse emissions. The widespread use of products such as D5 Green and Neocrete Activator has the potential to help reduce New Zealand’s carbon emissions from concrete. These products’ have strong export potential to the world’s largest concrete users such as China, India, the US and the European Union (Callaghan Innovation, 2021).